Designing the life science laboratories of tomorrow
In a world hungry for cutting-edge scientific research and development, life science laboratories are in high demand. Identifying the right spaces to nurture innovation – and fitting them out flexibly and sustainably – offers opportunities for the construction industry to deliver exciting new projects.
The UK is regarded as a life sciences powerhouse. Medicinal and pharmaceutical products are among the country’s top five exported goods, and the nation comes second only to the US in terms of inward investment.
The UK government values the domestic life science sector at £94 billion, and estimates it provides over 250,000 high-skill jobs in fields such as drug discovery, diagnostics, MedTech devices and vaccine creation. It is an expanding science, encompassing fields such as AI, genomics, biomanufacturing, tech-enabled healthcare devices and personalised immunotherapies.
The ‘golden triangle’ of London, Oxford and Cambridge is home to some of the most significant and well-funded universities and research centres in the world – all of which demand access to best-in-class life sciences laboratories. Universities and businesses in other parts of the UK are also hungry for lab space.
What are the characteristic design features of laboratories?
Lab fit-outs typically consist of a physical laboratory space area where research is carried out and an office-style ‘writeup space’, for performing desk-based analysis.
However, unlike office spaces, there are no accepted guidelines, specifications or building standards for life science laboratories. Despite sharing many common features such as receptions, desk space and communal staff areas, and even though they are often based in the same building, laboratory occupiers generally have different needs to those of office workers.
Many specifications refer to BCO Office 2019 as guidance for the office element, with no real set guidance for the laboratory function.
Confusion is also rife in how to deal with what is included within the shell and core of the building, and what is required as standard within the tenant demise.
The way life science companies operate within a building is also evolving. The incubator model – common in the US – is now gaining traction in the UK. In this model, multiple fledgling start-ups work in the same building and utilise the same facilities.
This one-stop-shop concept provides flexible, low-cost lab space and support to develop early-stage research. In addition to shared services, incubators can provide support to access venture funding, legal and IP guidance and commercial mentoring.
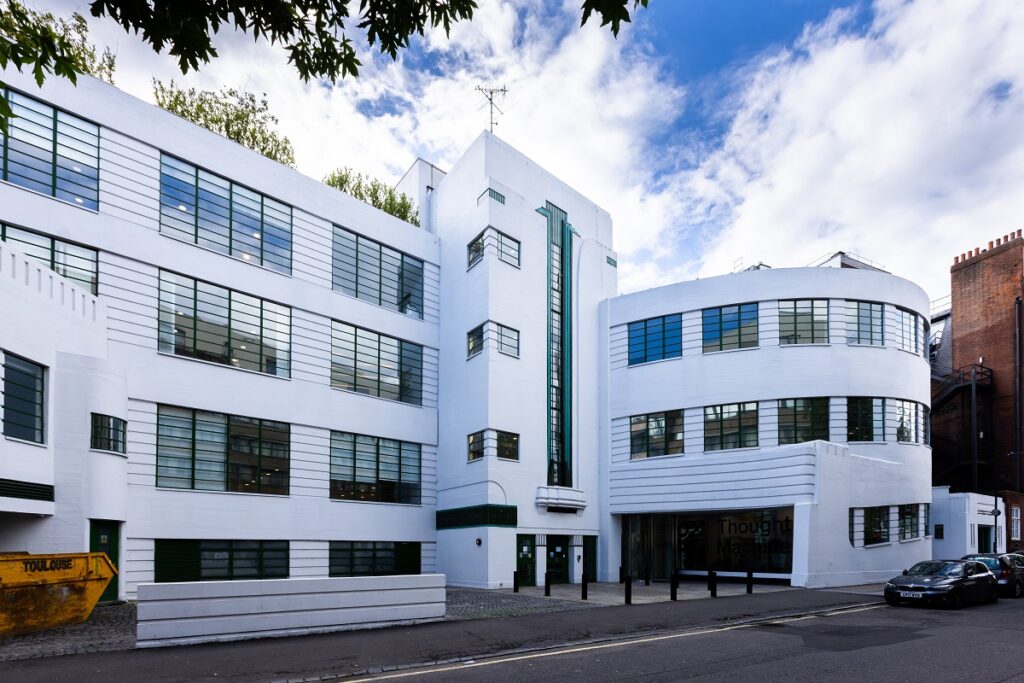
Designing with a solutions-focused lens
Some features and equipment common to laboratories are standard parts of a lab fit out specification. These include fume cupboards, door seals or multiple door systems, and writeup space.
It is generally considered wise to keep laboratory and office writeup space adjacent to each other to encourage the cross-pollination of experiments, research, and reflection amongst peers. A typical lab/office ratio is around 50:50. In projects where labs and offices are kept separate from each other, tenants have reported difficulty in effectively collaborating.
The access requirements must be considered well before the installation phase of a fit out. Particularly large or unique pieces of equipment may require specialist installation or be difficult to transport, lift or move, or may need to be built in situ. In some cases, rooms or buildings are designed around a specific piece of machinery. This can add to the building’s weight and structural loading considerations, including anti vibration measures, plus floor-to-floor height.
The more specialist the equipment, the more likely the requirement to provide special measures to control the environment in which the equipment is to be located – for instance slab thickening for vibration control, dark rooms, and clean rooms.
In turn, room heights often need to be higher to accommodate additional MEP needs. From a safety perspective, labs usually require high levels of ventilation and in some cases, advanced air filtration. There needs to be more frequent air changes in a science facility compared to an office space.
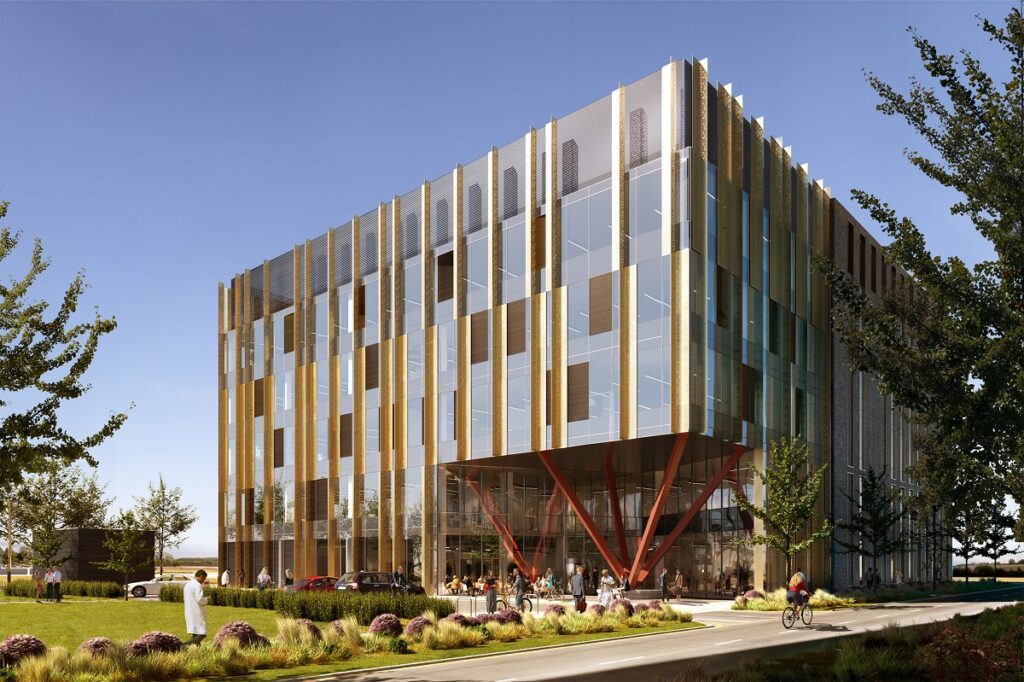
Prioritising health and safety is crucial
Containment levels – the ability of a lab to contain key biological hazards, genetically modified organisms and chemicals – must also be taken into consideration. These range from containment level 1 (C1), which represents the lowest level of risk, to containment level 4 (CL4), where highly dangerous or exotic microbes or pathogens are present, which currently do not have vaccines or antidotes.
At any containment level, laboratory doors/entrance systems need to be sealed and airtight. There are different ways to achieve this, but a common design is to create a double-door entry system.
The risk of containing potentially dangerous materials also makes building security a key design consideration. This extends beyond the labs themselves, to building reception areas and external spaces. Depending on the levels of security required, this will add significant costs on to a project.
Waste disposal is also key, and subject to hazardous waste regulations. Storage is also required for products such as consumables, glass products, personal protective equipment (PPE), and scientific literature. This can significantly increase storage space demands compared to a typical office.
‘Dry’ labs – used for computational science or advanced mathematical analyses – will require appropriate mechanical and electrical installations. Equipment such as 3D printers, powerful computers and lasers all demand specific power, safety measures, air supply controls, emergency power and humidity levels to function successfully.
Occupancy levels tend to be lower than typical office standards, between 15 – 18m2 per person, which impacts key services such as WC/shower provision and lift capacity.
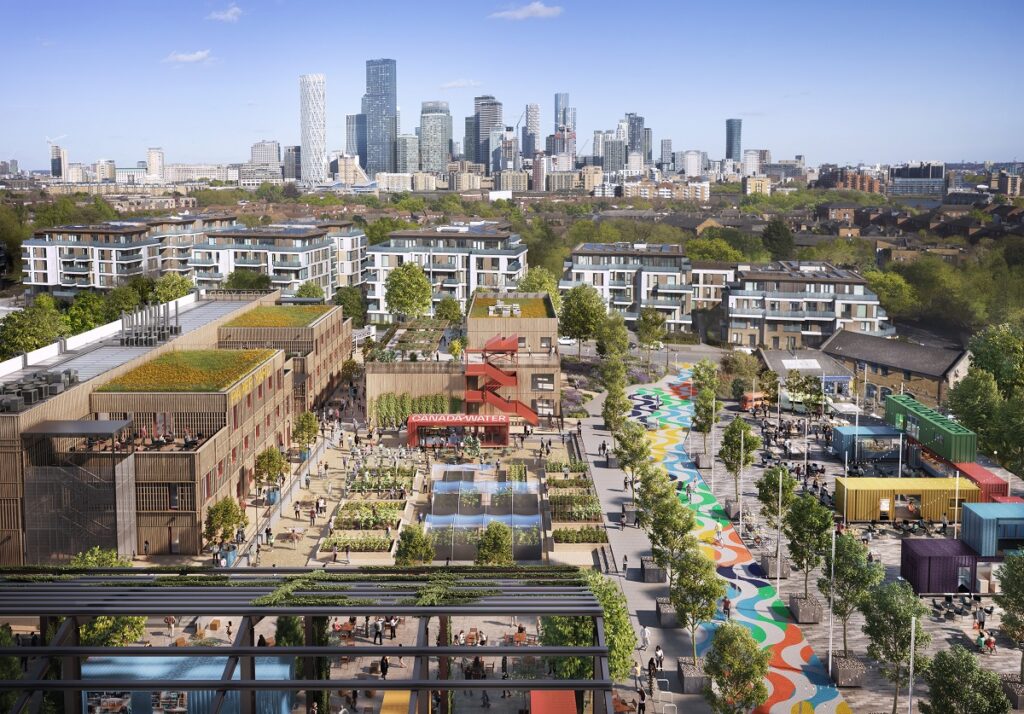
Meeting the growing demand for lab space
The sector is a hot asset for private investors. A record £2.5 billion in venture capital (VC) was invested into private UK biotechs in 2021: a 79 per cent increase on the total raised in 2020. Overall, this signals that life science companies in the UK are now strong targets for both state and private capital and suggests demand for lab space is unlikely to abate in the short term.
As new science clusters emerge outside of the golden triangle, major new projects are springing up around the country, with big-name international businesses making the UK regions their home.
Life science laboratory fit-outs must be adaptable and able to meet the needs of biotechnology start-ups, which are by their nature nimble, ambitious and fast-growing. They demand high-tech, high-spec working environments where they can meet and collaborate with their peers.
Strong sustainability credentials are also key. The challenge for the design and construction industries is to keep pace with the scale and ambition of the life sciences sector – creating laboratory spaces that help accelerate and support scientific progress.
Cost model: Laboratory fit-out
We have built a cost model for a fit-out to a newly built office/laboratory building, from shell and core in central London. The building has approximately 100,000ft2 of net internal area, with an assumed typical floorplate of 50 per cent offices, 50 per cent wet CL2 laboratory. The main floorplate has been assumed to be divisible by four tenants per floor. The design of the building assumes a 6.9m x 9m structural grid.
You can download the cost model here.
This is an abridged version of an article that was first published in Building magazine. You can read the full article by clicking here.