Designing logistics centres that can keep pace with demand
A trifecta of inflation, materials and labour shortages are stretching developers of logistics centres – yet despite the challenges, demand remains high. AECOM’s James Morrison, Gary Marshall, James Cooney and Matt Timms discuss how the industry is responding.
After a turbulent period which started with Brexit and was sustained by coronavirus, materials, labour and supply chain issues have now been ramped up by the conflict in Ukraine. Wider economic inflation, in turn, is driving costs to all-time highs.
Yet the most surprising thing about the logistics market at present is that it is buoyant in the face of these staggering materials price hikes. The industrial market has experienced double-digit increases on build cost over the past eighteen months – leading to an incredibly challenging time for market participants, where demand is high, but supply of key elements is low.
Logistics buildings typically have a very simple design, comprising an envelope of structural steel, a concrete slab, and then cladding on the walls and roof. However, with steel and concrete now in high demand and low supply, logistics centres’ need for large amounts of steel means costs and delays have become particularly pronounced. Steel and concrete are also energy intensive products to produce. As energy pieces rise, production costs have also soared.
How inflation impacts procurement
The typical procurement route for this building type is changing. A previous preference for single-stage tendering is now changing in favour of two-stage tendering, and to a more partner-based approach. Many of the bigger developers are even bypassing two-stage tendering – instead, going straight to a partnership with a contractor at an early stage, in order to try and lock in prices and contractor availability.
January 2022 saw some of the sharpest materials price increases on record. To offset building costs, rental prices are rising on units. This shift in yield has helped upcoming and in-development projects to continue to be financially viable. The problem developers face doing deals going forwards is how to predict build cost, and whether deals can be achieved on a fixed-price basis.
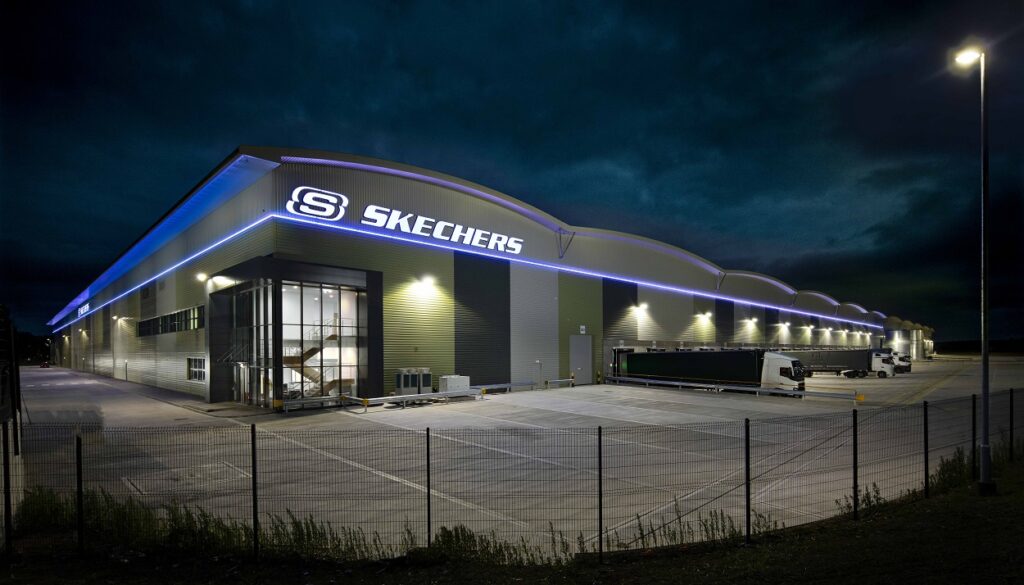
Design with end use in mind
The biggest change with this building type over the past decade has been the shift to ecommerce, which now dominates demand. All retailers are assessing their ‘dark lstores’ and last-mile facilities and want to use them to help gain a competitive advantage over rivals – by ensuring their logistics centres enable the fastest and smoothest order fulfilment.
While logistics centres are relatively simple in design, there are differences in facility layouts and heights based on what stage and type of fulfilment they are catering to. Last-mile logistics centres typically have a ground-based operation inside the building. They do not require high racking and are often laid out like a supermarket, with staff doing the picking rather than shoppers. In contrast, larger distribution centres, perhaps leased or owned by major international online retailers, feature high bay racking, and often deploy greater levels of technology and robotics for picking products.
Therefore when developing a shell, it is important to consider the expected end use. For example, a fulfilment centre which has heavy amounts of robotics may need to reconsider the use of roof lights, windows, and sources of natural light, which can confuse robot tracking and motion sensors.
Amenities for the people who working in logistics centres are improving, as labour shortages make it more important to attract and retain workers. Some core features are found in almost every project – such as a canteen, showers, changing and toilet facilities, and a large car park. However, gyms, sports fields, trim trails and additional EV charging points for staff cars and grassy outdoor meeting or relaxation areas have all been included in recent projects, to attract tenants and retain labour.
To maximise value, some tenants are opting to make their distribution centres also their HQ or primary office location. This may also drive-up demand for enhanced staff amenities and increased office design. Offices are typically fitted out to Cat A.
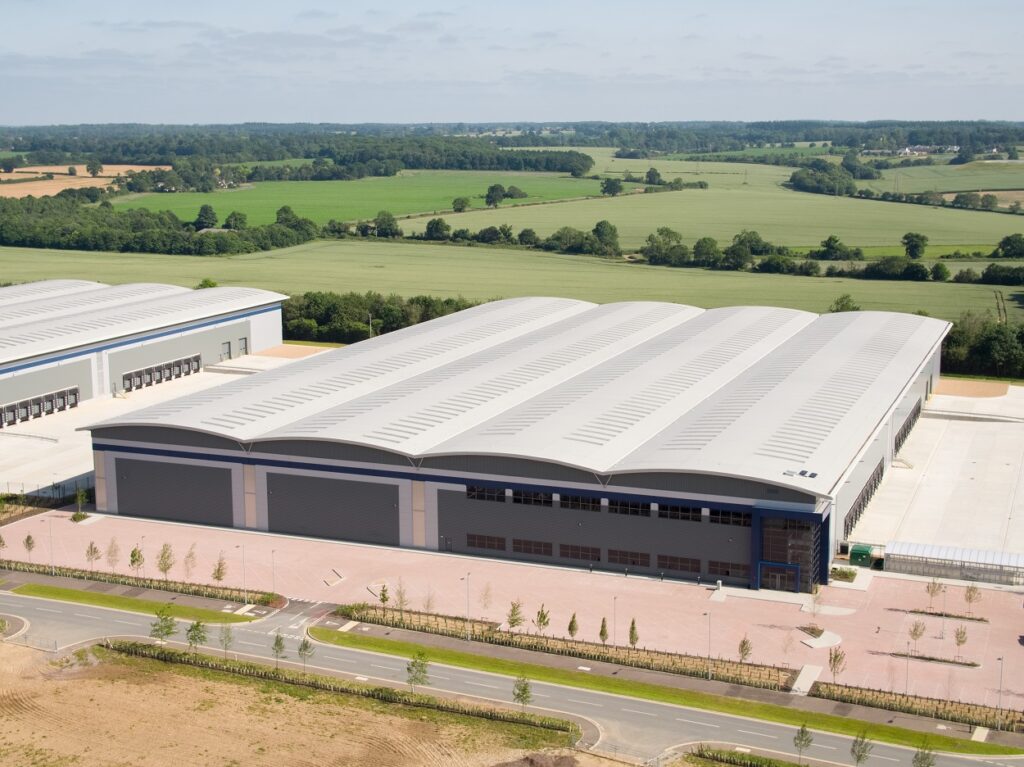
Making logistics centres sustainable
Because logistics centres are such large, open spaces, the cost impact to improving sustainability is relatively small compared to the cost of the building itself. BREEAM Very Good is easily achievable with speculative logistics developments, and is now a baseline; BREEAM Excellent status is also being reached on some projects where tenants have demanded it.
Logistics centres, with their large flat roofs, are obvious choices for solar PV installation and this is now commonplace. Some developers are selling the electricity generated from their rooftops to tenants. Making logistics centres self-sufficient from an energy perspective will likely become a strong selling point soon.
Location also informs what sustainability measures can be included. Rainwater harvesting, on-site wind turbines, EV charging points at every delivery van space and water attenuation are all being deployed on projects.
A smarter and more efficient future
Rather than a case of ‘survival of the fittest’, where only the largest contractors or tenants can take on and manage the risk associated with the inflation happening on these projects, it may turn out to be survival of the smartest – those industry players who can collaborate with the right partners; secure prices, labour and materials as efficiently as possible; and keep watch and respond to the retail trends which are influencing demand for these buildings.
Cost model: Distribution warehouses
We have built a cost model for a shell logistics building in a central UK location. The parameters are set around a gross internal area (GIA) of 159,900ft² (14,855m²), including a 475m² office fitted out to category A, powered by a pure electric system. Unit rates are derived from competitive design and build tenders and current at 3Q 2022.
You can download the cost model here.
This is an abridged version of an article that was first published in Building magazine. You can read the full article by clicking here.