A sign of things to come
As the digitisation of industrial processes gains pace, we catch up with Lanner’s Chief Operating Officer Andrew Aitken for his view on Industry 4.0 and how businesses can best respond.
What’s driving the Industry 4.0 revolution?
Industry 4.0 is about much more than promoting change through technology. The Industry 4.0 vision of connectivity and digitisation was created in response to the threat of disruptive market forces, such as an aging world population and the rise of emerging markets. Flagged by global management consultants McKinsey & Company several years ago, it forecast that the next Industrial Revolution was imminent and would impact industry on a scale 3000 times greater than the First Industrial Revolution in the 18th and 19th centuries.
Fear is a great motivator and companies are now concerned about the rapid changes they’re seeing. They also see companies around them suffering as a result of new disruptive business models. A good example is what’s currently happening to many banks as a result of digital payment systems, such as Apple Pay, which lets users pay for goods using their phone — it’s a sign of things to come.
How is Industry 4.0 changing the industrial sector?
Industry 4.0 is creating a buzz, a purpose and urgency. It demands that we consider new ways to move towards more connected, intelligent and agile business models if we are to compete in tomorrow’s markets. Industry 4.0’s arrival should be welcomed. Many firms have been focusing on short-term performance goals due to uncertain global economic conditions, forgetting about the bigger picture: Industry 4.0 is a useful beacon for these businesses to consider where they are now and how they should best respond.
In light of Industry 4.0, manufacturers have started reviewing their IT infrastructures and technologies. The decisions that businesses make now will determine whether they are one of the quick or the dead five years from now. Ultimately, many of today’s successful manufacturers need to quickly and radically change their business models to succeed in tomorrow’s global marketplace.
What are some of the big challenges businesses face as industrial processes become even smarter?
Securing and retaining industrial vendor and client intellectual property (IP) are well-documented challenges that will require commercial and technical effort from businesses at the outset but these are likely to become more manageable with time.
The biggest challenge for companies will be recruiting, developing and retaining a truly smart workforce capable of understanding and running complex Industry 4.0-like business operations. The skills transition required at all levels, particularly within senior decision-making teams, will be challenging. Traditional management principles will become obsolete, with rear-view business intelligence data becoming less relevant as decision making becomes more agile, powered by front-view predictive analytics.
How can businesses future‑proof their processes and facilities??
Senior management teams need to stick to the basics, starting with an assessment of their current technology and people capabilities, before setting expectations. It’s also valuable for businesses to compare themselves against known competitors and industry best practices. They can then stress-test how their business and technology strategies currently align with Industry 4.0 by conducting a strengths, weaknesses, opportunities, threats (SWOT) analysis and by prioritising risks and opportunities as a driver for recalibrating their aspirations for the next one, three and five-year horizons.
To reduce the risk of costly mistakes in planning major process changes, businesses can use virtual simulation modelling software, such as Lanner’s WITNESS, to ensure that proposed changes will perform as expected when implemented. Virtual models also aid communication and collaboration with external technology implementation specialists and employees throughout the change process.
Most critically, businesses should recruit new talent who have the right balance of technology and problem-solving skills — the recruitment and development of a smart workforce is likely to be the most formidable Industry 4.0 asset. Through strategic and innovative partnerships, manufacturers, technology suppliers, research institutions and businesses can collaborate to share ideas, expertise and data to drive best practice, innovation and quality.
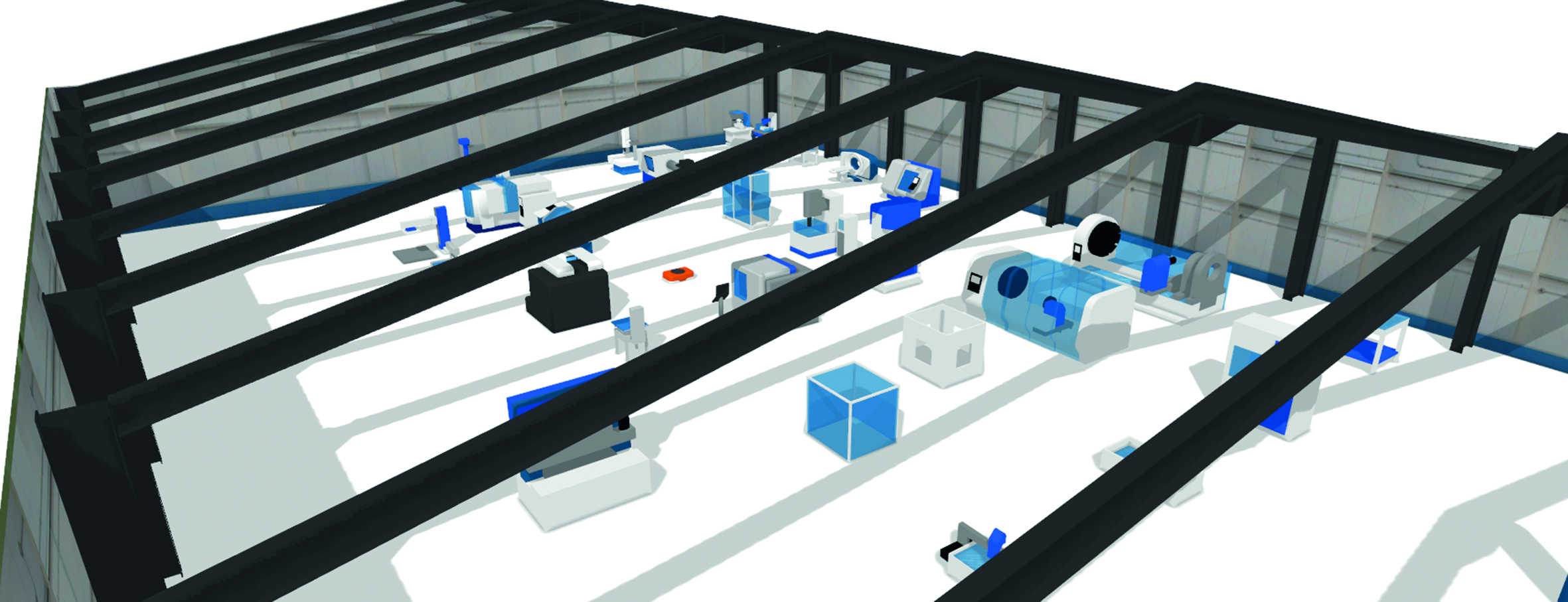
Simulating risk
With the launch of Facebook’s Oculus Rift and Microsoft’s HoloLens to the commercial market, and Apple’s announcement that it is also investing in virtual reality technology, immersive environments are becoming the next big platform.
Virtual simulation is expected to play an increasingly important part in the future of smart manufacturing. It allows businesses to create immersive replicas of entire factories, manufacturing processes and equipment and workspace layouts before they’re built or modified.
Using powerful virtual simulation software, process and automation teams can create a virtual ‘copy’ of an assembly line, for example, to test and understand how a new technology will impact production. This allows businesses to reduce the risk and cost of integrating the technology into their existing facility. Process simulation can also prove the benefits of process change and predict the likely return on investment, helping companies build the business case for continuous process improvement so they can stay competitive in the changing Industry 4.0 landscape.