Research to reality
Factory 2050 is one of the most advanced manufacturing research facilities in the world. Home to The University of Sheffield Advanced Manufacturing Research Centre (AMRC), the facility combines state-of-the-art digital technologies and flexible automation, and is set to revolutionise the way aircraft are made. Take a tour with AMRC’s Ben Morgan as he offers his insight into future aerospace production.
The aerospace factory of the future will be reconfigurable and adaptable, says Ben Morgan, head of Integrated Manufacturing at Sheffield University and Boeing’s AMRC — the team behind Factory 2050.
“In aircraft factories, planes are traditionally constructed in big monolithic structures. These are bespoke to the products and rarely flexible between models. There’s definitely a swing towards plane assemblies themselves moving along the production line, with smaller, more flexible manufacturing systems coming in and performing a particular job, then moving away. This allows the same machine to be used for many aircraft models,” says Ben.
A buoyant market
Ben and his team of engineers are installing cutting-edge technologies, advanced robotics and flexible automation at Factory 2050, driving research into high-variation and mass customisation manufacturing. A global proving ground for automated and advanced manufacturing, the facility is a place where industry and academia can work together to develop and test new advanced manufacturing technologies and methodologies.
So what can we expect form aerospace manufacturing in years to come? “It’s a very buoyant market out there,” says Ben. “Airbus and Boeing’s single-aisle aircraft production rates are on the increase — they’re both manufacturing around 40 aircraft a month with the intention to move up to about 65 over the next few years. That’s a significant rise in production on what are already stretched land and machinery resources.”
More data, more uptime
Ben also predicts we’ll see a lot more data generated from aircraft in the years to come, which will ultimately help operators make decisions about whether their planes are fit for use or need maintaining.
“A Rolls Royce aero engine now has so many sensors that it produces around 20 gigabytes of data an hour. Aero structures will also have more integrated strain, vibrational and temperature sensors than ever before. Sensors will also become much smaller, cheaper and better-connected,” says Ben.
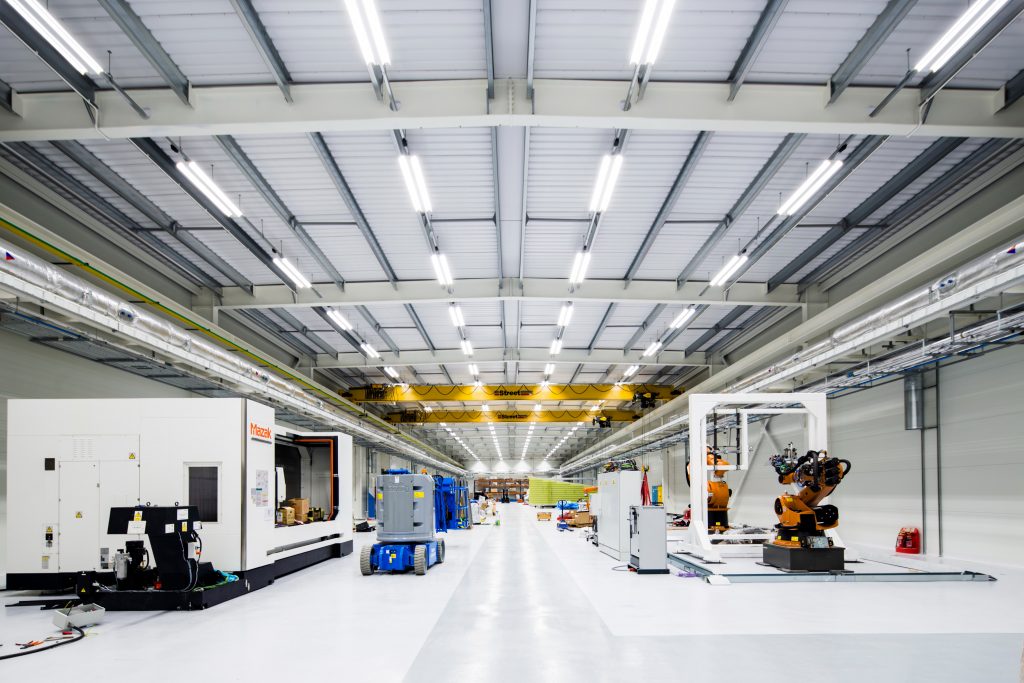
More intelligence?
While the future of aerospace manufacturing is set to become increasingly automated, the widespread use of artificial intelligence across the industry could be a little while off yet, says Ben. “Robotics and automation have been implemented across aircraft manufacturing for the past 10 years. However in terms of more intelligent systems that make decisions themselves, we’ll need a greater level of confidence in them before they become mainstream — but we could start to see them in them in the next five to 10 years,” says Ben.
Challenges ahead
Looking ahead, Ben believes legacy aeroplane models could make it trickier for aerospace businesses to become more digitally connected: “The A320 was designed in the 1970s so a lot of it still isn’t digitised. To have a smart, intelligent factory you need to understand the factory structure and the digital model of the parts moving around it. In many industries, particularly automotive, this is taken from granted. Legacy machines and the numerous variations of hardware suppliers into an aerospace factory can be a barrier to getting all the machines integrated and talking to one another,” adds Ben.
A Rolls Royce aero engine now has so many sensors it produces around 20 gigabytes of data per hour.

A learning curve
With Boeing and Airbus already 3D printing plane parts, the use of new and more lightweight materials looks to become more commonplace in both military and commercial aircraft production. But, there’s a way to go yet in terms of material standardisation and quality control.
“3D-printed products aren’t as structurally sound as forged or cast products. But, it’s a learning curve — a pretty quick learning curve. Carbon fibre, titanium and 3D-printed products are being manufactured for planes, and they’re stronger and lighter than they’ve ever been, helping with fuel economy and improving the overall quality of parts; the better the quality of parts, the more aircraft uptime,” comments Ben.
Playing catch up
As aerospace looks to become more automated, the industry is starting to attract highly-skilled staff from the automotive sector. “Aerospace is catching up and trying to learn from car makers as to how they’re doing it (automation) so well. But automotive, food and beverage and other industries can learn a great deal about traceability and quality from the aerospace industry — the safety qualification that goes into a plane is absolutely paramount. The way they deal with traceability is absolutely fantastic,” says Ben.
Investing in the future
Ben’s advice to manufacturers as they start planning to become more digitally connected, is to have a strong strategy in place for product development. He comments “businesses need to ensure their IT structure links very closely to their manufacturing strategy, because smart, digital factories will be so integrated in the future that the two will go hand in hand.”
“They also need to take the customer and the supplier along for the ride, and make sure they’re moving at the same speed”, adds Ben. “Because it’s no good having a digitised factory and still having orders faxed through. Businesses should also start investing in training and apprenticeship schemes to bring the right staff through with the right skills.”
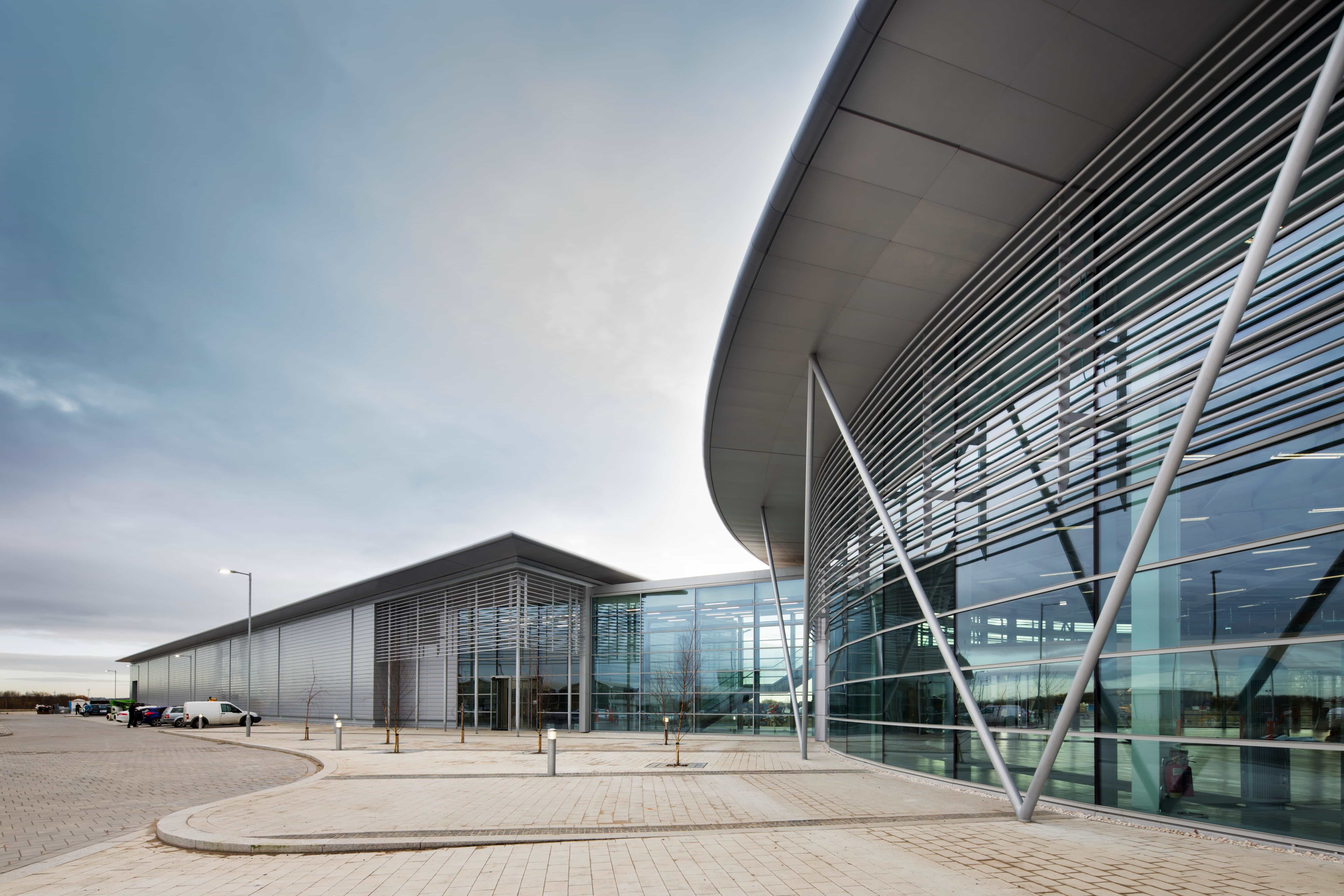
AMRC’s Factory 2050
The University of Sheffield AMRC with Boeing is a world-class centre for advanced machining and materials research for aerospace and other high value manufacturing sectors.
The AMRC team are carrying out research at Factory 2050 in response to the increasing requirement to rapidly change product designs and switch between making high value components and one-off parts for customers from diverse sectors.
Initial projects include a programme to take aerospace manufacturing technology into the construction industry, explore future digital factory technologies for building commercial aeroplanes and investigate digitally-assisted assembly technologies which could help to fill a looming skills gap in the aerospace sector.
The £43 million, 7000 square metre building is constructed largely from glass, and is partly funded by the European Regional Development Fund and the Higher Education Funding Council for England.
AECOM works with AMRC through a unique innovation partnership, combining factory design experience with Factory 2050 research, to deliver advanced manufacturing to real-world industrial projects.