Getting the most out of ground investigations on major projects
Ground investigations on large-scale schemes are growing in complexity with managing contractors appointed to coordinate the huge amount of data generated so that accurate and detailed information can be fed into subsequent phases. Yet, an ‘intelligent’ managing contractor can bring far more to the table than just data assurance, says environmental contracting specialist David Ridout.
The early bird catches the worm. This is certainly the case on major infrastructure projects where ground investigations are concerned. Information collected during ground investigations can add tangible value to a project in several ways – but only if the data collected is managed effectively. A managing contractor will coordinate operations to get this done but whether further benefits are achieved from the ground investigations phase, such as collaborating with stakeholders to limit potential construction issues or improving safety standards to reduce risk onsite, is down to the managing contractor’s approach.
The challenges and benefits of data collection
First, let’s examine the benefits of good data, and why it can be a challenge to capture. The data collected from ground investigations underpins the successful creation of a new built asset, or characterisation of an existing asset, by providing critical information that feeds into the planning, consenting, design, procurement and construction phases.
Additionally, ground investigation data is of enduring value to the asset owner after construction. The data needs to be retained appropriately, readily available in the right form for use in ongoing asset management, enhancement, replacement or decommissioning, though arguably this benefit is not as recognised as it should be.
Frequently, despite these benefits to project delivery, large scale ground investigations are not prioritised or managed efficiently enough to harness, form and retain good datasets. This is especially true for major projects where ground investigations are growing in complexity. From archaeology and ecology to remediation and hydrogeology, there can be a huge range of specialist teams and contractors working on site. Maintaining a high standard of fieldwork delivery and ensuring data product consistency and assurance becomes a huge logistical challenge that clients often don’t have capacity to meet, thereby missing out on a huge opportunity to maximise the data collected to improve delivery certainty and enduring value.
What do we mean by ‘intelligent’ managing contractor?
Clients can appoint a managing contractor to oversee and coordinate the ground investigations and related survey work. A managing contractor will organise the multiple companies into an integrated coherent team working under one roof, with single point accountability. Onsite processes are standardised, and information consolidated so that it is easily and readily accessible to the client, resulting in greater data assurance to harness the benefits mentioned above.
But more can be done: if a managing contractor works intelligently, these good data management practices can be amplified to create a culture of collaboration that brings other benefits, such as encouraging early contractor involvement to give greater cost assurance.
Additional benefits around health and safety can be harnessed as a one-team approach can be leveraged to improve all-round safety standards thereby reducing risk onsite. Not only that, the sharing of best practices contributes to the betterment of the construction industry as a whole so that the project leaves a tangible legacy.
“If a managing contractor works intelligently, good data management practices can be amplified to create a culture of collaboration that brings other benefits, such as encouraging early contractor involvement to give greater cost assurance.”
This article explores these added benefits in greater depth. We draw on our experience as principal contractor overseeing the ground investigations on Highways England’s Lower Thames Crossing (LTC) project – which, once complete, will be the longest road tunnel in Britain – to highlight the many advantages of taking a smart approach to the role of managing contractor within a real-life complex infrastructure scheme.
Five benefits an ‘intelligent’ managing contractor can bring to major schemes
1/Greater collaboration
A management contractor is able to take a holistic approach to a ground investigation programme, ensuring consistency and generating a collaborative spirit so that subcontractors work as one team.
Under this approach, all parties – including the client, subcontractors and other stakeholders such as landowners and statutory bodies – are on the same page from the outset and expectations are better understood. For example,
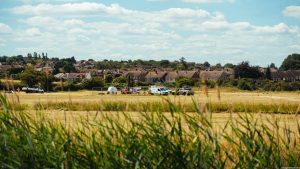
we facilitated an overall planning meeting at the start of the LTC ground investigation programme, and – for the first time in a major ground investigation campaign in the UK – used early contractor involvement (ECI) and a two-stage contract. This enabled better planning, organisation and processes to be driven throughout ground investigations from start to finish. For example, through ECI we were able to determine fieldwork duration and costs before we executed very large ground investigation contracts and launched onsite.
Through collaborative working, the LTC ground investigations obtained vital data to limit potential construction problems and gained the consent of over 90 per cent of landowners on the route – an incredible feat, considering year-long delays have hit some major schemes because the land access was not in place. All this increased certainty around design approach and construction costs.
For optimal collaboration, daily dialogue with key parties is imperative. This means any potential issues – such as land access or the need to change route – can be communicated upstream to the client or downstream to other subcontractors, via a project manager.
2/Streamlined and efficient approach to the delivery of multi-disciplinary investigation
Ground investigations on major programmes require a bespoke response best met through the establishment of a lean Programme Management Office (PMO) to steer the array of projects that can then be sized as packages of work to suit individual contractor delivery capabilities, geographic area or technical need.
The most effective way for a managing contractor to conduct ecology, archaeology and ground investigations is to coordinate teams in a single campaign so that disruption and cost are minimised.
3/Integration of ground models under one roof
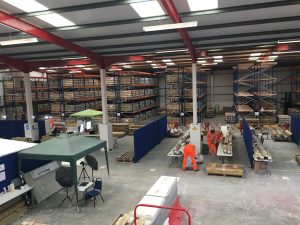
Integrating the ground models for archaeology and geotechnics can bring significant efficiencies. On LTC for example, we fully integrated types of samples and cores collected for ground investigations with geoarchaeology, which were then logged and sub-sampled geo-technically and geo-archaeologically in a central store located in the main compound. Moving away from geoarchaeological monitoring in the field has other advantages, too – multiple cores were logged per day rather than just one and there was no danger of aborting work and lost archaeologist days in the event of a rig breakdown.
4/Optimised data management
With an ‘intelligent’ management contractor instilling best practices, co-ordinating the ground investigation processes, enabling knowledge sharing and driving greater collaboration, it follows that the information gathered will be better managed.
Even so, the correct data management tools are still needed to handle the significant volume of data generated. On the LTC ground investigations, we used tailored data management tools that allow multiple users to upload data, deliverables and information, which become available immediately. Information from site was captured and saved in a centralised database, allowing for standardisation of information records including common referencing and structure.
Furthermore, effective data management systems are important for data collection and distribution, providing progress monitoring, and making information easily accessible to all parties as a single trusted source. The use of such tools reduces cost and saves time through streamlined processes developed through lean management.
The tools are also used from a safety and wellbeing perspective, as they provide up-to-date information on access routes and approval of permits. Personnel fatigue is also tracked.
5/Improving safety and reducing risk
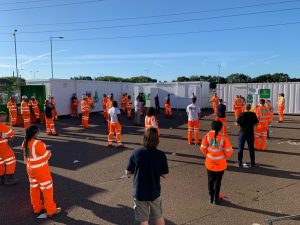
Whether contracted to or not, a management contractor is in a strong position to drive significant health and safety improvements. Working collaboratively, it is possible to boost the skills of everyone involved in the supply chain by setting high health and safety standards and best practices, achieving a safer site, thereby reducing risk.
For example, we lead an industry working group that has developed a complete series of operating standards which apply safety first principles[1] and these standards have been offered and adopted by clients, designers, contractors as part of their promotion and intent in levelling the field for contractors to price safety into ground engineering projects without the fear of being undercut. On LTC, we also developed a digital gateway permit system which ensures full compliance at each stage of the planning and works execution process to eliminate human error and the negative outcomes which can result.
A collaborative environment can drive health and safety improvements in other ways too. Our work with contractors and manufacturers on LTC has led to the development of innovative new tooling and equipment, such as the Long-handled LayKey and Release Tongs used within the wireline rotary drilling process, which ensure that the support operative’s hands remain 250mm away from entrapment points, dramatically reducing the risk of hand injury.
All told, constructors and designers are waking up to the importance and benefits of ground investigations, particularly for large-scale projects. The added value that an ‘intelligent’ approach can bring is hard to ignore.
Case study: Successfully managing ground investigations on the Lower Thames Crossing
Once complete, Lower Thames Crossing will be the longest road tunnel in Britain. As principal contractor on behalf of Highways England, we undertook phased ground investigations across Kent and Essex across an area exceeding 7,500km. We were responsible for more than 20km of drilling, employing at peak some 50 drill rigs, and in excess of 10,000 individual tests involving a team of more than 1,500 colleagues.
Once on-site, we implemented a considerable number of lean management tools, so that all parties operated as efficiently as possible, generating approximately £5 million in savings for the client. AECOM was rated 3.3 out of 4 – matching the highest ever score – in the Highways England Lean Maturity Assessment (HELMA) against a wide range of lean and continuous improvement principles. These included leadership and engagement, understanding customer value, benefit realisation and delivery, and supplier maturity.
As a result of our initiatives to drive safety improvements, we were awarded the prestigious Ground Engineering Health and Safety Award in November 2020 for the site-specific audit and inspections regime. The judges stated that the programme was: “A great initiative which has benefited the project, but also the wider industry. It is clearly focused on improving Health and Safety standards in ground investigation, using innovative techniques to implement the approach. The involvement of all stakeholders and those in the supply chain created a collaborative project at all levels of delivery.”
[1] consisting of Rotary Drilling, Cable Percussion Drilling, Trial Pitting and Dynamic Sampling