Making lean leaner
The Lean Enterprise Research Centre suggests 60 per cent of production activities do not add value to the end product or customer. Process and automation engineers Robert Davies and Stephen Mounsey look at clever tools and techniques that reduce wasteful parts of systems, and how coupling them with digital processes can drive improved production.
What is lean manufacturing?
Lean manufacturing involves using tools and techniques to identify and remove waste such as time spent waiting between production stages or during product transportation, with the ultimate aim of creating more value for customers.
For manufacturers and service providers, applying a lean approach to business operations essentially makes production more efficient throughout the entire value chain to increase overall productivity and margins. Lean asks businesses to ask themselves: how can we improve the way we make our products? How can we provide customers a better service?
Who created lean?
Lean thinking can be traced back to Henry Ford who, in 1913, introduced the Powered Assembly Line, where machines used to build the Ford Model T were arranged in the correct production sequence to create flow, from the collection of raw materials through to car delivery, bringing great efficiencies.
By the 1930s, Ford’s work had revolutionised both American and European manufacturing and led directly to the development of the Toyota Production System, which shifted the focus from mass production to gain economies of scale to creating linked efficient production processes that produce goods at the rate of customer demand.
Since then, hundreds of publications have been written about lean thinking, most significantly Daniel Roos, Daniel T. Jones, and James P. Womack’s The Machine that Changed the World, published in 1990.
Today, lean approaches are used not only across manufacturing but the construction, aerospace, ship building, administration and health industries.
People, not just process
Lean manufacturing isn’t just about making individual parts of a process quicker or more efficient; a truly lean business works to reduce waste in every part of the organisation from accounts to logistics.
People play a big part in making lean work — if employees don’t understand lean, why it’s important and how it works, it will be difficult to implement it within any business. Communication and encouraging lean thinking through training is a good place to start.
Our lean training helps managers understand the benefits of applying lean to the workplace by tailoring the training to their company.
We work directly with organisations to understand their concerns with their current operations, analyse their processes and then use this information as the central case study in the training. Our bespoke approach helps our clients understand the potential benefits of lean in relation to their specific business operations and needs.
How do you apply lean on the ground?
There are a number of lean tools and techniques that can be used to identify and eliminate production waste and optimise manufacturing processes. We explain four of them in more detail below.
Root Cause Analysis – A process that identifies the underlying cause of a problem to prevent it from happening again, rather than fixing it each time.
Visual Factory – The use of visual tools such as photographs and graphics to communicate information about a process such as how to use it and help drive efficiency.
Kaizen (Continuous Improvement) – A strategy where employees work together proactively to achieve regular, incremental improvements in manufacturing processes.
Mistake Proofing (Poka Yoke) – Simple methods for eliminating errors in product design and manufacturing processes through error detection to achieve zero defects.
How does Industry 4.0 enhance lean?
The use of smart, digital processes such as simulation and automation, which we’re seeing with Industry 4.0, are all part of the lean evolution; both lean and Industry 4.0 set out to make industrial processes faster and more efficient and produce higher-quality products using fewer resources.
The digital revolution has for the first time enabled the real-time capture and seamless input of customer data into product and service design, shrinking production time from concept to delivery.
Smart technologies give manufacturers and service providers greater control over their processes. Sensors built in to production equipment gather real-time data, speeding up the transfer of vital process and product information, detecting potential production problems immediately, which can then be resolved sooner, reducing process down time. Increased data and digital connectivity can also directly control inventory levels, materials and transportation flows to match the rate of production, eliminating overproduction and extra processing.
A smart way to cut time and add value
We’re using lean thinking and process simulation to help our marine client refurbish and refit their customer’s ships, taking two and a half years per vessel instead of three.
Through detailed process analysis we’ve identified that the heavy lifting equipment they use to move ship parts to storage on a dry dock before they’re sent off for refurbishment, is needed for just five per cent of the items. The remaining parts weigh fewer than 10 tonnes and require a much smaller, lower tonnage lift and conveyor system, with the current system taking an unnecessary amount of time to move the items from A to B, causing delays and bottlenecks, adding no value to process or our client’s customer.
To ensure the new lifting and conveyor system works as efficiently as possible, we modelled the equipment flow through the dockyard using Lanner’s Witness simulation software. The simulation pinpoints if anything could potentially interfere with the process and slow things down or cause congestion such as the location of storage areas on the dockyard, and things like how many fork lift trucks are needed to move the equipment around the dockyard.
By reducing and removing waste from the process, we’re helping the client cut their refurbishment programme by around 15 per cent, or six months, as originally set out, bringing the ships back into service sooner.
This not only saves the customer enormous sums of money but adds value too.
By incorporating smart technologies and RFID (Radio Frequency Identification) tags into the process, the customer can also digitally identify, track and locate the items, giving them more control throughout the entire refurbishment process.
With six more ships due for refurbishment over the next 20–25 years, more efficient equipment flow across the dockyard will save the customer time, resources and money well into the future.
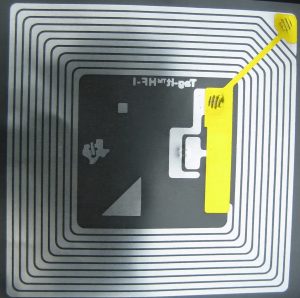