MMC and the New Hospital Programme: unlocking the limitless potential of prefabrication
The United Kingdom (U.K.) government’s Construction Playbook and modern methods of construction (MMC) may be must-haves on the New Hospital Programme in England, but the construction industry is arguably not yet ready to deliver MMC at scale or pace.
For this reason, there’s a danger that expected cost and programme benefits will not be realised. Faced with this stark reality, it’s up to designers to think, act, embrace and implement MMC in the form of ‘Hospital 2.0’ to ensure the construction industry and ultimately the National Health Service (NHS) gets value for money, argues healthcare engineer Adam Bradshaw.
With 41 new hospitals in the pipeline and a funding envelope to the tune of £45 billion, it’s no wonder that the NHS England team describes its New Hospital Programme (NHP) as the ‘biggest hospital building programme in a generation’. With construction commencing in three waves from 2025 to 2039, the Infrastructure Projects Authority and the NHP team are looking to MMC and Hospital 2.0 (a standardised design approach that supports faster delivery, improves productivity and ensures value for money) to shift the build programme into top gear.
The use of offsite construction and prefabricated components on healthcare projects is not new. From fully modular pandemic response facilities to internal fitouts, the use of prefabrication has saved the sector time and money. However, the NHP is unprecedented in size and scope — and this presents a potential problem, as the construction industry (and its supply chain) is not yet able to implement MMC at the scale and pace required. Progress is being made to invest and upskill, but designers recognise the utopian dream of a standardised approach that includes a library of components and widespread manufacturing facilities for prefabricated parts does not yet exist at the scale required, certainly for the early schemes.
For those early Wave 1 hospitals currently in the detailed design stage, there is a danger that MMC could be shoehorned into the design to increase the proportion of pre-manufactured elements without sufficient consideration of project specifics or the wider construction market, and the much sought-after social and programme benefits that we all seek from MMC will not be realised.
It’s up to the NHP, healthcare designers, and contractors to bridge this gap between expectation and reality to make sure that the NHS gets value for money not only on the first wave of hospitals, but also across the future pipeline, so that all 41 hospital schemes are delivered on time and on budget.
AECOM has embraced the principles of Hospital 2.0 on the first wave of NHP hospitals, which we hope will inform best practice on future waves. This article examines that approach in greater depth and explains why it is necessary in the current climate. We also discuss steps the construction industry could be taking to get the most out of prefabrication on current and future NHP phases, which has relevance across the wider pipeline of government-commissioned work.
Current context
By placing MMC at its heart and implementing the principles of Hospital 2.0, the NHP is following the best practice outlined in the U.K. government’s Construction Playbook. The playbook was published in December 2020 and contains government guidance on sourcing and contracting public works projects and programmes across 14 key policies, of which MMC is one.
To ensure the best practice guidance is applied consistently, government departments and arm’s length bodies are required to adopt the policies on a ‘comply or explain’ basis. Significant progress has been made in other sectors in adopting MMC principles and realising the benefits that this brings. However, a step change is needed to support delivery across the 34 hospital schemes in the next three waves, so they can comply with Construction Playbook best practice. With Hospital 2.0, the NHP has begun early engagement with the construction industry supply chain to establish “new standards to help standardise the design of new hospitals and make use of modular construction methods to speed up the build.”
Maximising the benefits of MMC
How engineers and designers respond to the challenge on the first wave of hospitals has implications for future projects, as it presents an important opportunity to influence thinking. Our specialist healthcare teams have demonstrated that MMC can bring real value when implemented appropriately; drawing on experiences from schemes where MMC delivered time, cost, and wider benefits that are derived from MMC such as at Clatterbridge Cancer Centre and The Grange University Hospital.
1/Taking a system-agnostic approach
Through the application of MMC on the hospitals that have already been built, we have seen significant benefits from an increase in construction quality through factory-controlled manufacturing processes and improved health and safety through to the reduction in material wastage and the potential for reduced carbon emissions. However, designing for specific MMC types can narrow markets, lessens competition, and increases risk in the event of failing contractors.
By contrast, a system-agnostic approach that encompasses all MMC typologies drives competition, increases innovation, and embeds efficiencies and benefits regardless of construction techniques. We must also consider the wider implications of increasing MMC to make sure the specific systems are used appropriately within the context of each project. Focusing solely on maximising the proportion of MMC can lead to missed opportunities and introduce inefficiencies. For example, on refurbishment projects within operational hospitals, designing modularised risers purely to increase MMC proportions would lead to increased embodied carbon for the module frames, and slow progress on site to thread the risers through a warren of existing services.
With the advent of Hospital 2.0 we are seeing that the NHP have recognised these challenges and is implementing a standardised approach that aims to allow some flexibility and not prescribe specific systems. For example, a standardised grid provides uniformity in room layouts and fit out but allows choice in structural typology. This will be balanced with other standardised components that are readily available throughout the supply chain such as pre-manufactured plant.
2/Embedding MMC principles right from the start
The supply chain is evolving rapidly due to the government’s mandate to embed MMC across its public sector programmes, but also in response to the pandemic, where off-site production is proving its worth over site-based activities.
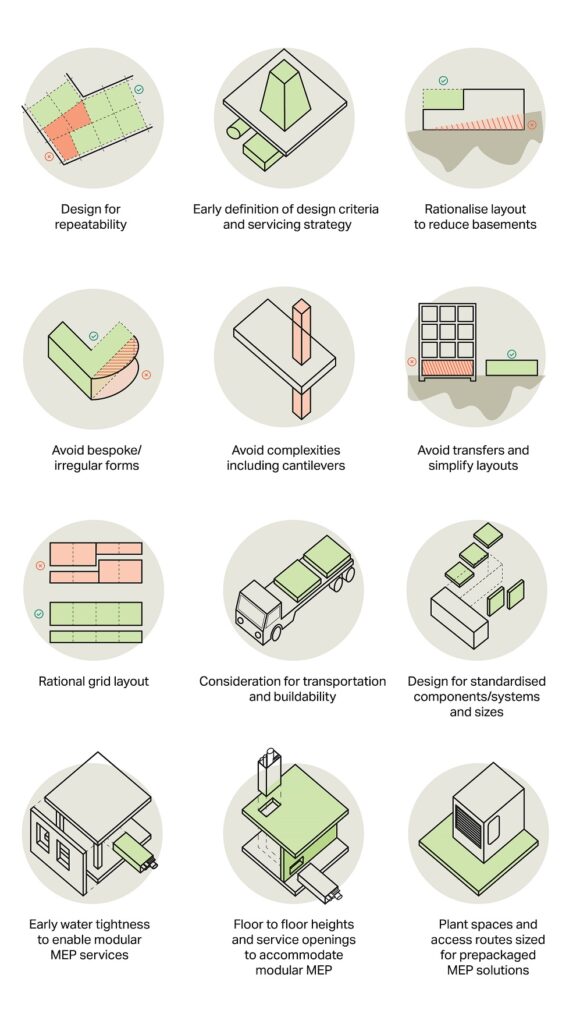
Unravelling designs to accommodate MMC at a later stage is inefficient and often problematic. These principles must be baked in at the start of the project so that they guide the design.
Doing this successfully involves developing a full understanding of the project and constraints. Individual project characteristics vary significantly — from topography to location and from refurbishment to new build schemes — so a thorough understanding will inform how and where Hospital 2.0 can be incorporated effectively.
Furthermore, optimising the design for Hospital 2.0 must be achieved without compromising clinical functionality or operational efficiency. Working with the NHP advisors and committing to collaboration across all NHP schemes through sharing expertise and combining knowledge is critical.
3/Engaging with the supply chain
The supply chain is evolving rapidly due to the government’s drive to embed MMC across its public sector programmes, but also in response to the pandemic, where off-site production is proving its worth over site-based activities.
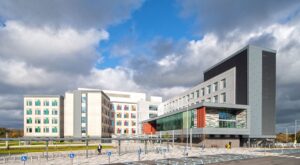
Engagement with the supply chain brought tangible efficiencies to The Grange University Hospital in Wales.
As the project’s building services engineer, we had taken a Design for Manufacture and Assembly (DfMA) approach right from the design stage, engaging with the contractor Laing O’Rourke and using its in-house component library. The resulting designs led to a 42-week (23 per cent) programme saving and reduction in 237,099 working hours on site. This was further improved to 52 weeks in response to the pandemic and a critical need for additional beds. Partial opening of the £350m hospital was achieved in April 2020, nearly a year ahead of schedule.
Ongoing engagement with the supply chain is therefore very important as understanding opportunities and constraints in this growing market informs designs. Through the formation of the Hospital 2.0 Alliance of contractors, a framework of contractors committed to working across multiple NHP schemes, this affords the opportunity to bring the benefits of MMC across all current schemes and build on the learning from wave to wave.
A careful balance needs to be struck between providing a wider spread of contractors to mitigate the risk of underperforming and failing contractors, or a contractor working on multiple projects to enable them and their suppliers to invest in MMC production, stimulate innovation, and provide consistency.
The current strategy for Wave 1 schemes is to assign one contractor per scheme, which presents significant challenges. These include sourcing enough contractors within the U.K. or internationally who have the capability and appetite to deliver complex healthcare projects and making all schemes commercially attractive to encourage their participation and re-engagement with the healthcare sector in England.
Despite these challenges, the level of risk associated with the NHP justifies this approach, making collaboration across contractors, suppliers, designers, and clients even more imperative. Strong collaboration is essential to share knowledge, optimise MMC adoption, and manage risks effectively across the programme.
The success of this model hinges on a robust and committed pipeline of projects in future waves, supported by sustained cross-party political backing and industry alignment.
Ultimately, this approach will help establish a resilient, efficient, and sustainable MMC-enabled supply chain capable of delivering the New Hospital Programme’s ambitious targets on time and within budget.
Further actions for the construction industry to take
Working with the Department of Health and Social Care, the NHS E/I and the NHP, here are three actions that the construction industry could take to improve MMC adoption of current and future phases.
Further engagement across NHP schemes
The gateways to allow projects to advance to the next stages and demonstrating a robust MMC strategy are now established with Hospital 2.0. The NHS E/I have also begun to engage designers across the schemes to find commonality or dissimilarity in their respective designs and gain benefit across the wider programme. Design teams must continue to collaborate and partner with the NHS E/I and NHP to drive wider Hospital 2.0 implementation across current and future schemes. Without this learning process, there is a danger future NHP scheme designs may have to be reviewed and reworked to increase proportions of MMC, which could delay delivery.
Collate data and a shared set of metrics
Collating real-world data across sectors will be pivotal in informing future MMC strategies. Metrics on waste reduction, waiting times, transportation distances, skills uptake, quality and defects, health and safety records, cost, and programme can all be used to correlate the effectiveness in the increase of pre-manufactured value (PMV) and compare against Hospital 2.0 objectives.
To achieve this, it is essential to implement a common digital framework that integrates data capture from the design phase through to construction and handover. Leveraging Building Information Modelling (BIM), digital twins, and interoperable data platforms will facilitate real-time tracking, benchmarking, and transparent reporting of MMC outcomes. This digital integration not only supports performance measurement but also enhances collaboration, risk management, and decision-making across the project lifecycle.
Review procurement routes
Future procurements and frameworks should support Hospital 2.0 with the development of a market and supply chain that can develop and deliver designs based on Hospital 2.0 principles, manufacture and supply components, and innovate to improve and develop over time.
The recently established Hospital 2.0 Alliance Framework (H2A Framework) exemplifies this approach by creating a multi-supplier framework agreement that enables NHS England to engage contractors with the expertise, capacity, and capability to deliver complex hospital builds and refurbishments at scale.
Finding common ground
Ultimately, to get the most out of Hospital 2.0, we advocate for the U.K. government adopt an open-source approach that employs a library of components or ‘kit of parts’, a ready stream of contractors and prefabrication facilities to manufacture these components, as well as a reliable workforce. This would require committed government investment, incentives, plus a strategic approach across all government departments on major capital projects.
Until such time, designers, engineers and contractors on the NHP must work together to find common ground to break down some of the barriers to rationalisation and repeatability that currently exist on the hospitals being built. If we take an open-book approach to capture and share data, we can build on efficiencies from project to project for the greater benefit of the entire health service.
This is an updated version of an article originally published in April 2022.