What to look for when considering modern methods of construction
Modern methods of construction are being used to deliver better housing, faster. As new products and solutions emerge however, local and city authorities, developers and housing associations are presented with a challenge: which one fits the project best? John Lewis, AECOM’s UK and Ireland Managing Director of Modular, and Andrew Partridge, Associate Partner at Rogers Stirk Harbour + Partners identify three factors to consider during the decision-making process.
In 2019, the Housing Communities and Local Government Committee clearly stated that “a significant proportion of homes must be built using modern methods of construction (MMC) if we are to meet the target to deliver 30,000 homes annually.” Developers, contractors and design and engineering consultants, have responded to meet demand with an array of solutions and products – from refurbished sea containers to fully customisable modules. The result is a transformation in the way that we deliver the UK’s housing stock.
Local and city authorities, developers and housing associations are gradually embracing the idea of using these new construction technologies for use on their developments. The next step is choosing the right solution for the project and wider community – an understandably tricky ask when we remember that these construction technologies are relatively new and the pros and cons of each are not always apparent.
The way forward becomes clearer when we ask: what ambitions can a given modular or offsite solution meet not only for the specific project but for the wider community as well?
Adoption in the UK
The £72 million investment injected into the Construction Innovation Hub by the UK government in 2018 to promote the development of digital and advanced manufacturing is paying off. Advances in Building Information Management (BIM) and generative design software are accelerating the adoption of manufactured offsite solutions. Supply chains are maturing in response and are better integrated at the design stages. There has also been an uptick in manufacturing expertise within the construction sector. Hesitancy and concerns around higher costs are shifting as these construction technologies become more widespread and cost effectiveness continues to increase.
As more options come to market, the benefits in terms of cost savings as well as the reduction time in the design and construction phases by up to 50 per cent compared to traditional build methods, are being realised by authorities, developers and housing associations, especially in the context of meeting the UK’s ambitious housing delivery targets.
Government agency Homes England has been an earlier adopter. Modern methods are being used to construct 1,500 homes across the country. Homes England has just commissioned a research study to test these emerging construction technologies on its sites and it’s hoped that the results will further encourage uptake of MMC in housing delivery by providing verifiable performance data to inform future decision making.
Decisions should be guided by data, but it is important to also consider how certain attributes can inform project-specific and community-specific ambitions, for example how net zero homes can contribute to a borough’s wider carbon reduction targets or whether a solution is flexible enough to fit a site’s constraints.
Three factors that should guide decision-making
Below, we explore three factors that we think decision makers should consider, and give advice on how to achieve these outcomes.
1/Quality and the importance of the ‘MMC mindset’
The prefabricated homes from the 1950s and 60s have cast a long shadow over the reputation of modular housing. Preconceptions around ‘box’ standardisation, bland exteriors and poor standards of insulations and finishes still linger. However, today’s architects are using modern construction technologies to produce end products that are far superior – and much more flexible.
Good design delivers high quality living spaces. Modern solutions can be adapted to maximise the number of homes on a site, deliver different space standards and support a wider range of tenures. External elevations can be chosen to complement the vernacular.
To best achieve these outcomes however, it is critical that a fully integrated team – from the clients and the design consultants, through the supply chain and construction teams – comes to the table from project kick off to agree and sign off on elements such as space, materials and intended use prior to production. This process requires a complete change of mindset that is radically different from traditional ways of working.
2/Take a fabric-first approach to deliver low carbon homes
Decarbonising the UK’s housing stock is a significant slice of the strategy needed to meet ambitions to reduce net greenhouse gas emission by 100 per cent by 2050. This means addressing operational and embodied carbon.
Design innovation and technological solutions are helping to bring about behavioural changes to lower carbon emissions. Building for 2050, a research programme led by AECOM and funded by the Department for Business, Energy and Industrial Strategy is identifying the drivers, demands and challenges to delivering low carbon homes. If we are to meet net zero ambitions however, an MMC fabric-first approach – i.e. maximising the performance of individual components and elements – is essential. Solutions that identify fabric-first factors such as insulation, airtightness, ventilation and thermal bridging and solar gain will inherently deliver low energy homes with reduced running costs.
3/MMC solutions can be leveraged to make a positive local impact
Social value has risen up the political agenda since parliament passed The Public Services (Social Value) Act in 2012. The UK2070 Commission’s report lays out plans to ‘level up’ regional inequalities across the UK, although it is light on detail. Nevertheless, on a local level, boroughs and councils have successfully implemented social value into their procurement processes.
The skills required for MMC differ from those used on a traditional construction site. Some modular system manufacturers provide on-site training and employment opportunities for the local workforce.
For example, AECOM and RSHP’s INNO offsite volumetric system is a solution which can be fully localised, unlocking employment and training opportunities in the community, local authority or city. Working alongside the INNO central assembly site in Nottinghamshire – otherwise known as the Centre of Excellence – satellite assembly units can be set up near or close to project sites. INNO works with local authority organisations or institutional associations to employ and train local people to help deliver the high-quality homes.
The importance of an MMC-mindset
Clearly, emerging construction technologies have potential to add value to an individual project and the wider community – and these attributes can inform the decision-making process.
To maximise that value however, traditional ways of working must be put to one side and a radically different mindset employed. Clients, design consultants, the supply chain and construction teams need to work together from the outset as an integrated team to get the best results. Delivering homes of a high quality must always be the priority.
Case study: YMCA Romford and INNO
Adopting the INNO solution – an offsite volumetric housing system by global engineering firm AECOM and world-renowned architects Rogers Stirk Harbour + Partners – the 39 one-bedroom units at YMCA Romford are helping residents take the step towards independent living.
The fabric-first approach to the design has delivered high quality and high performing homes which reduce the running costs for residents by 90 per cent and meet PassivHaus standards.
Working with INNO’s integrated design, manufacturing and assembly team, the YMCA adopted a MMC mindset that resulted in a clear design direction and an efficient delivery programme. As part of the process, a 1:1 digital model was produced and a prototype unit delivered prior to the production kick off, minimising snagging and defects to almost zero. These measures helped YMCA Romford make up to £250,000 in savings across materials, assembly and programme.
Steve Brightwell, Executive Director of Oerations at YMCA Thames Gateway commented: “At YMCA Thames Gateway we are committed to supporting our residents to move their lives forward, which ultimately means living independently. The challenge of providing high quality housing – that remains affordable – is well documented; and a key driver for us opting for the modular solution. Our new 39 units will provide young people with the incentive to become more independent whilst benefitting from a flexible, bespoke support package. Many of our residents can now cook their own meals, benefit from their own space, and a place to call their own. If we can start to develop more schemes in this way by using similar modern methods of construction – we stand a better chance at being able to house those that need a helping hand, rather than seeing so many sofa surf or live on the streets.”
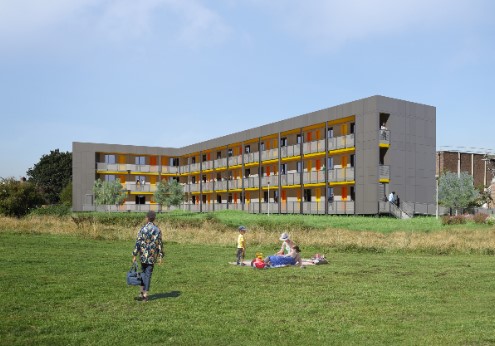
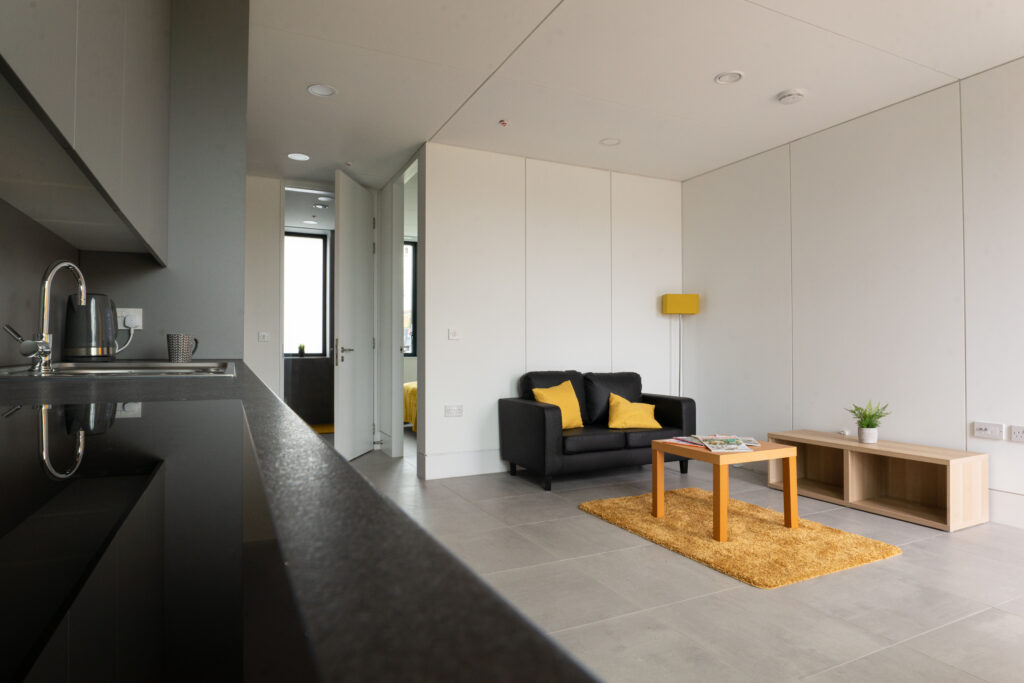