Net zero: How we measure the value of materials
Adam Parkes is a chartered member of the Institution of Structural Engineers and a member of European Federation of National Engineering Associations. Adam is a team leader from our London office, driving an initiative to ensure low-carbon approaches to building design through his role within our Net Zero Taskforce.
Imagine if we built a model in Lego or Meccano at home and then threw all the pieces in the recycling bin when we wanted to change our model. Wouldn’t that extra trip to the toy store be a bit wasteful and expensive.
We are all aware of the net zero challenge, in particular with the embodied carbon associated with structural frames. How structural engineers use their skill set and adapt is key to reaching net zero targets.
In the United Kingdom, our building regulations and legislation are becoming increasingly tighter from a carbon and environmental perspective and the targets for carbon emissions of buildings by 2030 are ambitious.
Across the design and construction sector, our consumption of raw materials is vast. In a future net zero world, it would be expected that purchasing high-carbon traditional building materials might come with a significant offset penalty. The question to ask is how are we considering the real value of these materials — especially in terms of their sell-on price and circularity?
The structure “is what it is”
Our default approach as engineers can all too often be tried and tested, and familiar to us. Material selection can tend to be based on nothing more than speed of design, familiarity of construction typology and the commodity of a competitive tender process.
If we seek to improve the industry environmentally, there needs to be a new way of thinking. A collective change in approach to the project brief.
Unfortunately for too long the structural frame and its construction materials are seen as “cost” outputs of the design process with little control — “it is what it is” I’ve heard some clients say.
Building materials and construction forms are still being specified without being challenged on what happens next. We need to start routinely addressing what happens at the end of the building’s life, who owns the materials during the building use and understand its potential sell-on value.
The London Energy Transformation Initiative (LETI) published data that paints a bleak picture demonstrating how embodied carbon consumption has remained relatively stagnant in our building designs for decades.
Targets require embodied carbon emission targets to halve current business as usual methods across almost all end markets. So how do we get there?
Procuring engineers early
One way to achieve these targets is by reclaiming materials, rather than buying new. Challenging the fundamentals of how we design our new buildings and investing more in a circular economy. Spending time to research and determine what materials are potentially nearby or on site, testing out the old Lego pieces and generating architectural form around them to accommodate the pieces we have would be novel and could be how we get close to ambitious targets without offsetting.
An adaptable building concept called Rightsizer proved that new ways of thinking can help us achieve LETI 2030 carbon targets in a tall residential building.
This project remains a concept idea, but it has proved that consideration of material sourcing and construction options at a very early stage can yield a step-change in building design. Engineers must be afforded an opportunity to work alongside an architect early — but it must happen at feasibility stage (Stages 0-1 in the RIBA Plan of Work 2020).
If we wait until RIBA Stage 2, then often the spaces, building heights and massing is already established and engineers can only try to fit structure into already congested bulk and mass. So by this stage, it is too late.
Introducing engineers as early as RIBA stage 1 could also lead to form-driven design adopting modern methods of construction with time to develop initial designs of key elements that would reduce waste, consider design redundancy and potentially reduce costs.
Building in redundancy for future adaptability potential perhaps defeats the object of reducing carbon in a time where we still use highly intensive carbon materials. Nobody yet can predetermine how soon it will be when low carbon materials form the majority of an engineer’s design for a building, but it’s likely technology will improve by the time a building needs to be strengthened for any future adaptability.
Building efficiently and reducing waste
Our buildings should be carbon-costed from day one. Engineers must consider end-of-life as the next most important aspect of good building design, targeting “dismantlability” and circular design principles.
We shouldn’t confuse re-use with recycling either. We know that reinforcing steel and structural steel gets recycled after the point of demolition — but as a process, this is an energy intensive activity as result of the transportation, and the shredding, melting, and refining processes.
Connection details should be with an engineer, not a contractor to ensure dismantlability is integral to the building frame design. Contractors have often reiterated that there is a misconception of economy in standardisation.
Adding steel-to-steel connection design to a consultant’s scope and designing them on a case-by-case basis using AI algorithms or dynamo scripts within our digital platforms can save significant waste generated through standardisation. The days where cost savings could be had by fabricating standardising connections are of the past.
Ethical sourcing of materials
In the food industry, we label the source of the product and its core ingredients. Is it not the time to do that for our materials?
Should we approach local manufacturing facilities and specify locally sourced material in our specifications where we can, and legislate around ethical sourcing in the UK to make it transparent?
Structural teams need to ensure early engagement with batching plants, steel fabricators and timber producers as we typically do with other specialist design items such as piling, secondary steelwork and waterproofing.
The benefits of encouraging off-site manufacture and modern methods of construction (MMC) over traditional methods are obvious, but let’s not stop at precast columns and cores. The majority of the embodied carbon of a building sits in the horizontal elements: slabs and foundations.
Moving forward starts at grass roots level and from the designers themselves. Target deadlines mean we can’t wait for legislation and each project has its own complexities so a standard brief will not always be the most appropriate route.
Initially designers could benefit from more time to consider novel approaches to construction, allow informed comparisons of the options, materials and quantities being consumed. This is where the industry must try harder to not rush into the construction phase.
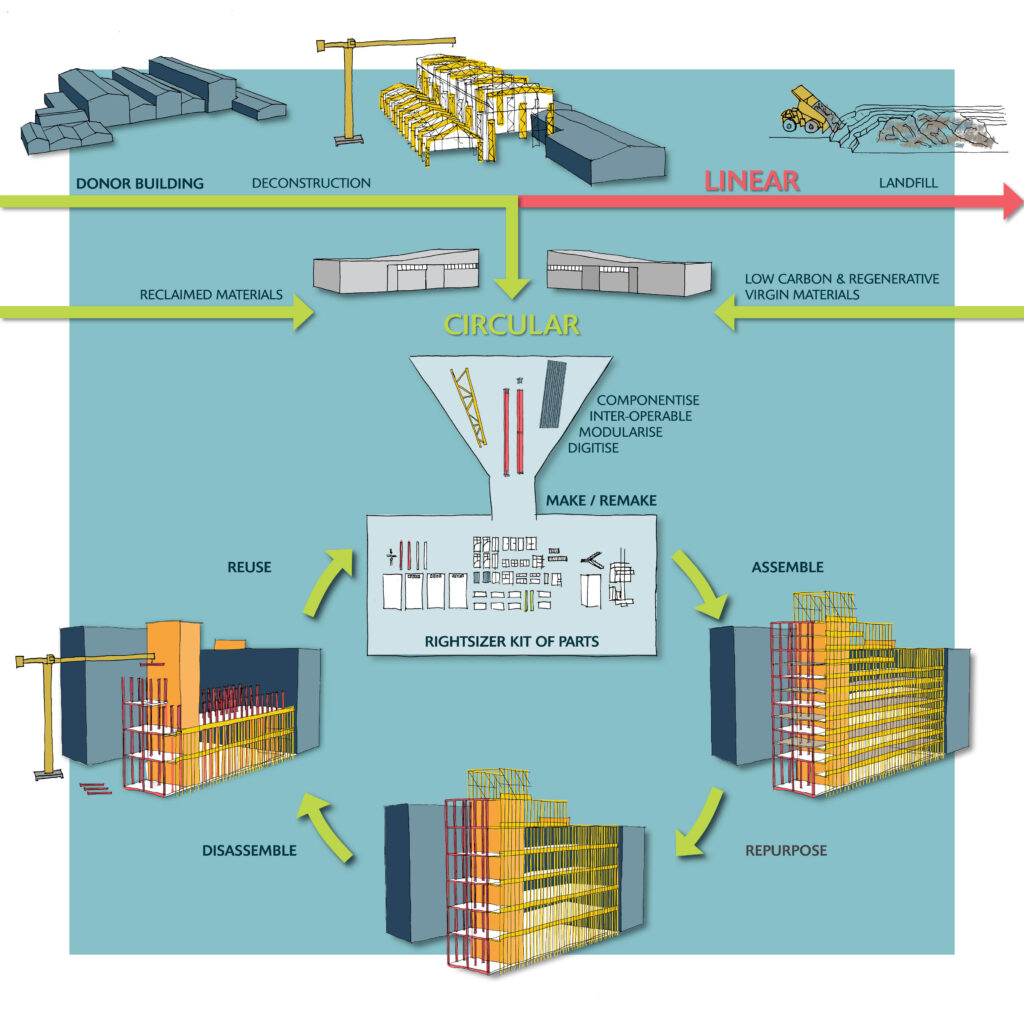
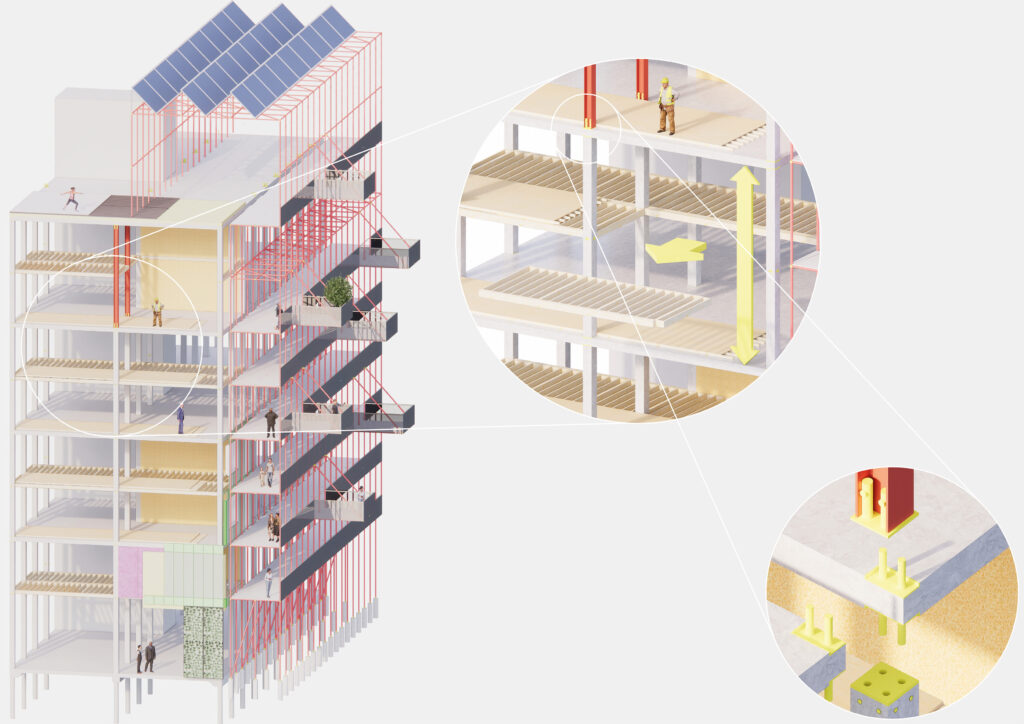