Building low-carbon commercial offices
When designing Grade A, low-carbon commercial offices, the industry is tasked with striking the most carbon and cost-efficient balance between re-use and adaption of existing assets and materials with introducing new elements, structures and materials on site.
Rising public knowledge and concern surrounding the climate crisis are placing pressure on developers to deliver decarbonised buildings. People are increasingly demanding that their workspaces align with their values: research this year by KPMG found that 20 per cent of UK office workers would turn down a job if a company’s environmental, social and governance (ESG) factors were deemed lacking. Almost half of workers want their employers to demonstrate climate and social commitments.
Progress is undoubtedly being made in commercial office space decarbonisation. However, a by-product of the numerous guidelines, targets, and standards created to help us reach net zero means that there is not one single accepted definition of what a net zero building is. There are varying, and at times conflicting, rules for the industry to adhere to.
Complicating matters further, these metrics and guidelines are constantly developing and being refined. It is therefore important to set clear objectives of what we are looking to achieve. One useful – and ambitious – metric is LETI’s upfront embodied carbon emission targets. These apply for building elements at the product sourcing and construction stage, excluding sequestration. This targets 350kg CO2/m2 by 2030, with 50 per cent of building materials from re-used sources and 80 per cent of materials used to be able to be re-used at the end of the building’s life.
As of 2023, this target is not being reached – 500kg CO2/m2 is considered best in class. We use the 500kg CO2/m2 metric as our benchmark for a low carbon building targeting net zero in this cost model.
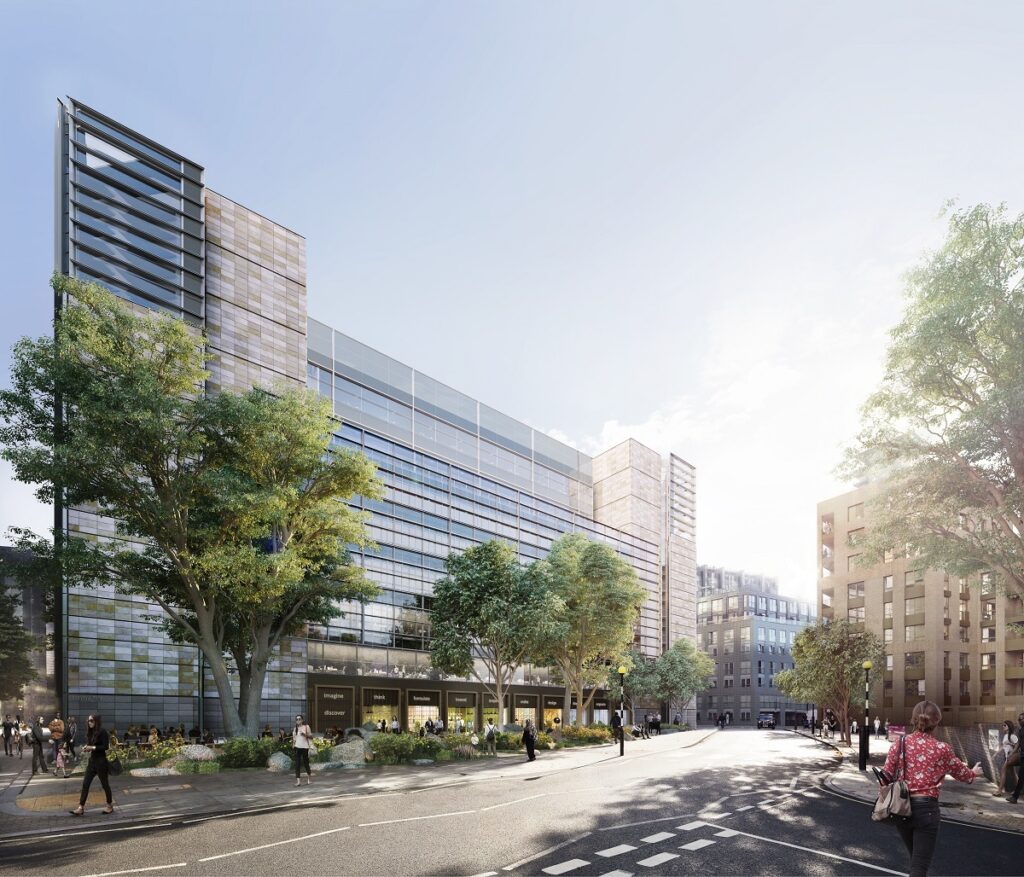
New build versus refurb
Embodied carbon is the most important and carbon-intensive factor to consider when designing for net zero. As the embodied carbon profile of a refurbishment project can be lower than a new build development, we are witnessing a shift towards a refurb-first approach to delivering projects across the UK. This is part of a general drive towards making the use of new materials in buildings a last resort, rather than first choice.
Yet choosing a refurbishment over a new build does not guarantee the lowest-carbon result. When measuring a project’s carbon profile, choosing between whole life versus upfront carbon measurements is a key factor to consider when trying to deliver the lowest carbon project possible. Typically, a refurbishment option will have a lower upfront carbon footprint. However, when assessing the whole life carbon of the building, the efficiencies associated with a new build scheme could close the gap.
Solid, accurate modelling and data are required to make sure the right assessments and choices are made as to whether to pursue a new build or refurb development.
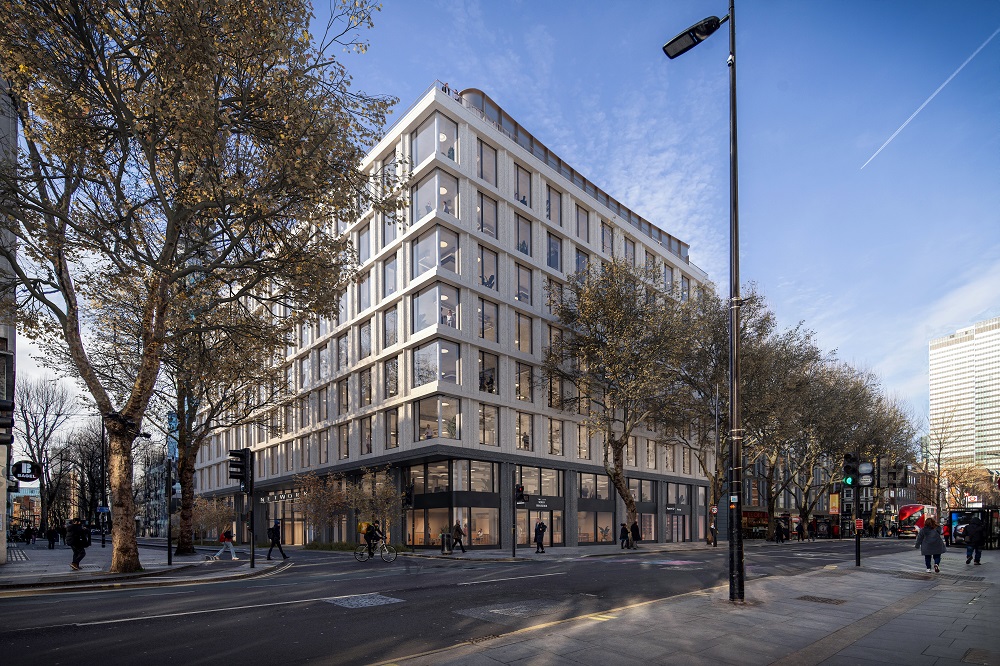
Design considerations
The market (developers, tenants, agents) perceptions of what makes a Grade A office space need to include sustainability credentials, but this may conflict with other aspirations, such as the desire for large, open plan spaces. To meet these sometimes competing demands, traditional specifications should be challenged.
If retaining existing buildings, reviews of the product and the specification level required – or that tenants are prepared to accept – are essential for a clear design solution to be achieved. Lateral thinking is important. For example, some schemes are now prepared to embrace smaller column grids and less stringent environmental conditions.
When deciding what to re-use, and what to build or procure as new, the following design factors should be considered:
Sub-structure
- Basements. Our preliminary research suggests a basement could emit the equivalent of between two and three storeys of superstructure frame based on a typical single-storey basement of a mid-rise residential building. The industry is increasingly looking at how the basements inherited on schemes can be incorporated and re-used.
- Re-use of existing foundations/pile. The cost and viability of re-using and strengthening existing foundations should be the first potential solution to investigate, as it reduces the need to build new. With new sub-structures, the use of hollow piles, which reduce carbon by cutting material volume, can be considered. Precast, reusable, UK-sourced commercial hollow pile products are growing in use and availability.
Structure/Frame
- Concrete. Reducing concrete through design measures is the most effective way to cut the carbon impact of a project. Where concrete cannot be re-used or, in a new build, reduced through design, products are emerging to attempt to reduce its carbon intensity.
- Steelwork. The carbon intensity is influenced by the amount of steel specified for a frame, so the design should aim to minimise the amount of steel used. Reused steel can have a carbon intensity as low as 50kgCO2e/t, compared with a sector average of 1740kgCO2e/t for new steelwork.
- Structural grids and depths. A key driver for inefficient structural frame design is the current aesthetic preference for open spaces and concealed structures. By reducing grids, up to a point, significant efficiencies in the structure will be found in both the superstructure and substructure.
- Cross-Laminated Timber (CLT). CLT is a glued product, which can make it hard to break down, re-use or re-purpose. This may act at odds with circular economy principles and the sequestration benefits may be lost depending on the building’s end-of-life scenario.
MEP
- Recent calculations by the GLA suggest that services contribute 21 per cent to the whole life carbon output of a building. MEP decarbonisation is achieved by challenging norms; and optimising the efficiency of kit and its usage and control.
Finishes
- Developers are examining how they can dematerialise projects, cores, landlord and common areas that have the basic structure as the finish, sometimes with an enhanced finish from the original basic structure, without having to add further applied finishes to structure, which adds carbon.
Making net zero offices commercially viable
Net zero office buildings must evolve from being theoretical, to fully realised. For industry, the challenge is balancing cost versus decarbonisation. The overarching question is, how can we achieve lower carbon buildings in a financially viable way?
Right now there are more questions than answers. Existing norms must constantly be questioned if effective, consistent progress towards net zero is to be made. By making the most of disruptive technologies; choosing the most relevant, adaptable, low-carbon materials and processes; and by committing to industry-wide collaboration, we can answer these questions.
Cost model: Net zero offices
We have built a cost model calculating the cost and carbon of a new-build ground plus eight-storey commercial office building in a central London location. The report also includes a table which summarises the cost and carbon for two options to deliver the same overall size office building: the first is a complete redevelopment demolishing the existing structure and building new, and the second is a comprehensive refurbishment where the existing structure is retained and extended to achieve the same overall GIFA of 232,000 square feet.
Click here to download the cost model.
This is an abridged version of an article that was first published in Building magazine. You can read the full article by clicking here.