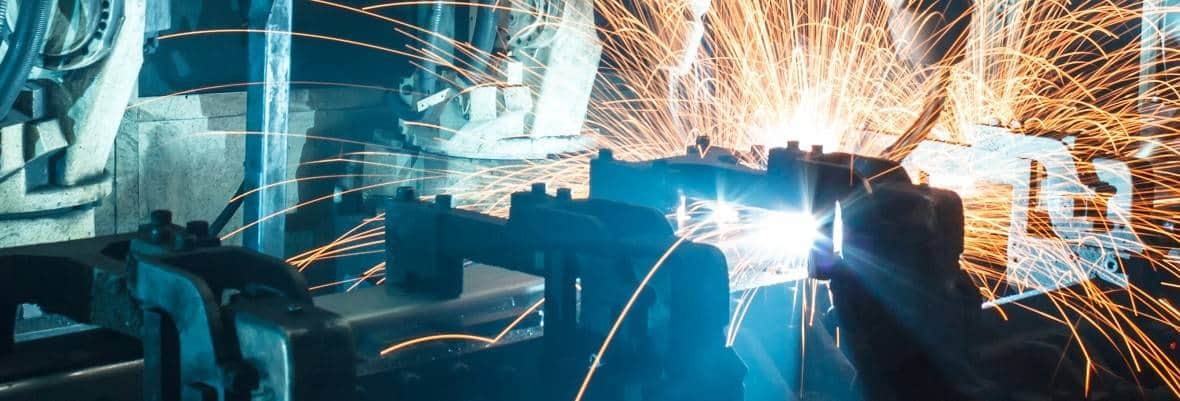
Process and automation specialists Eugene Smethurst and Stephen Mounsey talk us through the benefits of process-led design in making manufacturing plants more digitally connected, flexible and fit for the future.
Wanting the same as everybody else is no longer a customer’s greatest demand; tailored products are becoming just as important as good quality and price. Custom-made items have been around for some time now — Levi Strauss has been offering bespoke jeans since 1994 while Nike’s online service lets customers design their own trainers and bags.
One of the biggest changes we expect to see across manufacturing over the next decade or so is the shift from mass production to mass customisation, with Industry 4.0 being the perfect platform — and driver. Businesses that make the first moves to produce bespoke products en masse will undoubtedly face risks, such as not fully knowing the return on investment from new technologies. But, those who act quickly could add a premium of 30 per cent or more to their products, according to The Economists’ Made to order: Customisation advances in emerging markets report.
Old and new as one
Mass customisation will ultimately result in more complex customer orders with higher specifications. Each order will need to connect with supplier, product, production and distribution data in real time, meaning entire supply chains will need to be digitally networked, and equipment intelligent and adaptable enough to switch between designs and materials. To do this, factories will need to be smarter and much more flexible.
One of biggest concerns for manufacturers will be how to integrate all of this into what they’ve already got with as little cost and disruption to production as possible. Through optioneering, businesses can figure out how flexible their factories are. Using design and engineering tools, the optioneering process involves exploring different options to ‘bolt on’ new systems or processes to determine which ones will have the least impact on production and which ones will bring the most benefit.
Start as you mean to go on
Making a factory smarter is easier to do at the design stage, primarily because you don’t have to cut into what’s already there, so there’s no disruption to production.
Historically, the shell and process inside of factories have been built separately. But, by looking at the key parts of a process and integrating the building design so they work as a whole, you can drive greater efficiencies across an entire plant.
For example, factoring the outside temperature and building insulation into an automotive factory design could reduce the amount of energy — and cost — required to heat and cool the room where cars are painted.
More efficient plants have fewer process steps or more work done at single production stages, leading to a reduced floor area. Using a process-led design approach, it’s possible to streamline a process, increase the density of operations, integrate automation and digital connectivity, create meaningful spaces for people to work and collaborate, as well as factor in flexibility for the future.
Optimised process layout
The Gross Internal Floor Area or internal floor space is a good indication of a factory’s efficiency — more efficient plants have fewer process steps (or more work done at a single station), which leads to a reduced floor area.
By reconfiguring a leading car manufacturer’s process, we developed plans for a new factory that would reduce their existing internal floor area by 38 per cent.
After mapping out the crucial parts of their process, such as automation, people, production time and parts storage, we figured out where the processes could be reconfigured to optimise the process, floor space and overall operations.
We also identified ways to digitally connect everything, such as by integrating smart sensors and cloud storage, and areas where the process and factory could be easily expanded in the future. These included:
- Identifying where manual processes could be replaced with automation to increase productivity and quality.
- Integrating automatic guided vehicles or ‘mobile robots’ capable of quickly reconfiguring parts of the process.
- Introducing innovative energy sources, such as solar panels above the factory paint shop, where energy use is highest (around 40 percent of the factory’s entire power use), reducing energy costs.
- Increasing the number of people at each station from two to four without using more floor space by designing split level working, as well as parts delivery from above.
- Reconfiguring process layout to reduce the number of transfer conveyor belts needed, optimising process time.
- Curving the process layout to allow more parts to be delivered directly into the production line and the option of attaching a supplier park in the future.
- Integrating radio frequency identification tags, remote smart sensors, automated machines and cloud data storage to generate and capture vital design, customer product specification, production, material and supplier data.